یونیت نیوماتیک
طراحی مدار و ساخت یونیت های کنترل (تابلو) پنوماتیک و الکترو پنوماتیک
در طراحی سیستم های نیوماتیک توجه به عدم وجود نشتی، لوله کشی صحیح، کوتاه بودن مسیر هوا، سایزینگ درست شیرالات مورد استفاده و راحتی نگهداری و تعمیرات از اصول اساسی است.
بر همین مبنا شرکت نیوان با طراحی و ساخت یونیت(تابلو) های نیوماتیک کامپکت، این امکان را فراهم آورده است تا علاوه بر عملکرد دقیق و مناسب سیستم، فضای کمتری اشغال گردیده، مسیر انتقال کوتاهتر شده و همچنین از نشتی هوا به کمک لوله کشی مناسب جلوگیری گردد.
در صورت تمایل مشتریان، طراحی مدار پنوماتیک (مطابق شرح فنی و عملکرد مدنظر از دستگاه) توسط واحد فنی-مهندسی شرکت نیوان انجام میگیرد.
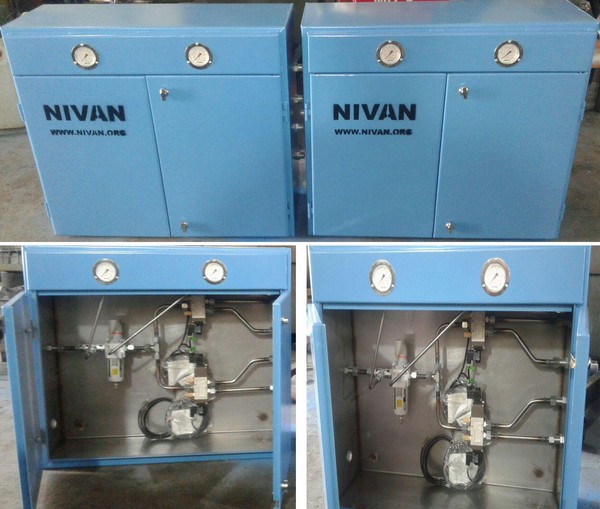
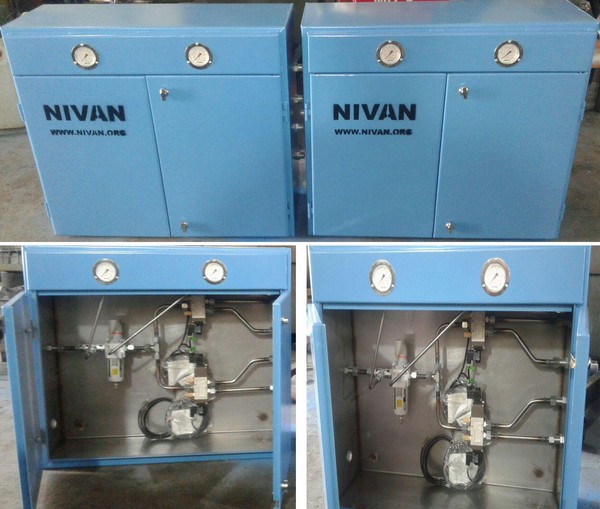
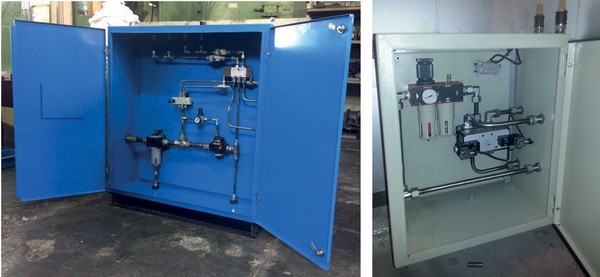
بلوک و زیرشیری هیدرولیک
صفحات زیرشیری و بلوک (منیفولد) نصب شیرالات هیدرولیک
نحوه اتصال و قرارگیری شیرالات در مدارهای هیدرولیک تاثیر بسزایی در نحوه و سرعت عملکرد سیستم، سهولت و هزینه های تعمیر و نگهداری دارد. استفاده از صفحات زیر شیری و بلوکها(مانیفولد) جهت نصب شیرالات درسیستمهای هیـدرولیک مـزایای بسیاری رابه همـراه دارد. ازجمله کاهـش حجم لوله کشی، کاهش نشتی، کاهش فضای اشغال شده، افزایش سرعت عملکرد و پاسخ زمانی، سهولت نصب و تعویض شیرها.
در این رابطه شرکت نیوان به ارائه محصولات و خدمات ذیل می پردازد:
ساخت بلوک و صفحات زیرشیری تک طبقه |
---|
در تمام سایزها("1/4 الی "1/4 1) |
مخصوص انواع شیرهای کنترل فشار، کنترل جریان و کنترل جهت مدل بلوکی و یا مادولار |
![]() |
ساخت بلوک های طبقاتی مخصوص شیرهای سایز "1/4 (( ISO/CETOP 03 |
از 2 تا 7 طبقه |
![]() |
![]() |
ساخت بلوک های طبقاتی مخصوص شیرهای سایز "3/8 (( ISO/CETOP 05 |
از 2 تا 6 طبقه |
![]() |
![]() |
طراحی و ساخت بلوک و منیفولدهای خاص جهت نصب یکپارچه و فشرده انواع شیرالات
طراحی و ساخت بلوکه و مانیفولدهای خاص از جنس فولاد یا آلومینیوم از دیگر توانایی های شرکت نیوان می باشد که به واسطه آن ميتوان انواع و تعداد مختلفیاز شیرالات با نصب بصورت سرراهی(خطی)، مادولار، بلوکي یاکارتريجی را با کمترین حجم لوله کشي و در کوچکترین فضای ممکن به یکدیگرمتصل نمود
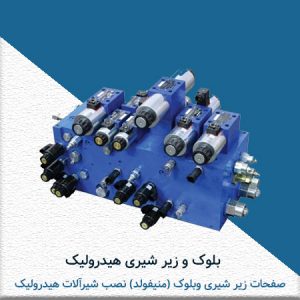
نمونه پروژه های انجام شده
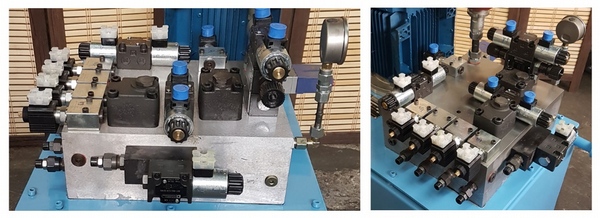
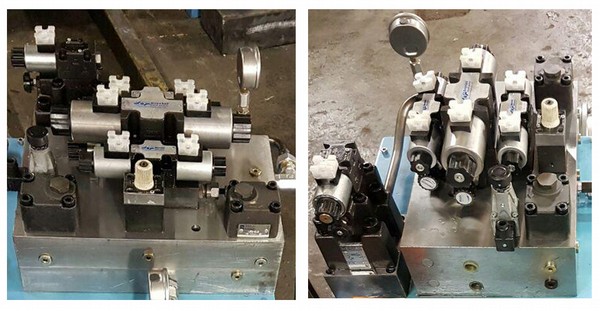
نصب ، شارژ و تعیین سایز
نکاتی در رابطه با (( نحوه نصب ، شارژ گاز و تعیین سایز آکومولاتور پیستونی هیدرولیک ))
نصب:
قبل از مونتاژ یا دمونتاژ آکومولاتور در یک سیستم هیدرولیک، فشار هیدرولیک سیستم بایستی تخلیه شود.
قبل از جداکردن اجزای آکومولاتور، مطمئن شوید که فشار در محفظه روغن و گاز تخلیه شده و شیر گاز باز باشد. قبل از بازکردن و جداسازی درپوش های هر دوسمت، به کمک یک میله از حرکت آزادانه و بدون مشکل پیستون اطمینان حاصل کنید. با توجه به خطرات احتمالی، تعمیر آکومولاتورهایی با پیستون گریپاژ شده، باید تنها توسط کارشناسان دارای صلاحیت انجام شود.
تحت هیچ شرایطی نباید بر روی بدنه آکومولاتور پیستونی، عملیات جوشکاری یا هرگونه فعالیت مکانیکی صورت گیرد. زمانیکه آکومولاتور پیستونی به مدار هیدرولیک متصل میشود بایستی سیستم کاملا هواگیری شود. هر گونه عملیاتی بر روی سیستم هیدرولیک(تعمیرات، نصب گیج فشار، ...) باید در زمانی انجام شود که فشار روغن کاملا تخلیه شده است.
شارژ گاز:
نیتروژن با خلوص %99.99 با سطح تمیزی > 3 میکرون استفاده شود. هرگز از اکسیژن استفاده نکنید(خطر انفجار!)
تعیین سایز آکومولاتور پیستونی هیدرولیک :
متغیرهای موثر در تعیین سایز آکومولاتور:
1- آکومولاتور پیستونی هیدرولیک با گاز نیتروژن شارژ اولیه میشود بطوریکه پیستون کاملا بر روی درپوش محفظه روغن چسبیده و پورت اتصال روغن را میبندد.
2- حداقل فشار کاری باید تقریبا 5 بار بالاتر از فشار شارژ اولیه گاز باشد. اینکار سبب میشود تا هنگام تخلیه روغن داخل آکومولاتور و حرکت پیستون به سمت درپوش سمت روغن، از برخورد آن با درپوش و همچنین افت ناگهانی فشار روغن در سیستم هیدرولیک جلوگیری شود.
3- در حداکثر فشار کاری سیستم هیدرولیک ، حجم گاز با فشردگی کامل آن به حداقل ممکن رسیده و حداکثر حجم روغن در آکومولاتور ذخیره میشود.
هنگام ورود روغن به داخل یک آکومولاتور پیستونی گاز شارژ شده در سمت مقابل منقبض و فشرده میشود و در مقابل هنگام خروج روغن از آکومولاتور پیستونی گاز در سمت مقابل منبسط میشود. از آنجاییکه فشار در سمت روغن و گاز تقریبا یکسان است و میزان تغییر حجم گاز در حالت فشردگی یا انبساط با حجم روغن ورودی و خروجی برابر است، لذا تغییرات حجم و فشار گاز معادل تغییرات حجم و فشار روغن است.
فرایند ایزوترمال: در این نوع فرایند تغییر فشار و حجم گاز به آهستگی و بدون تغییر در دمای گاز صورت میپذیرد(دمای ثابت گاز)
فرایند آدیاباتیک: در این نوع فرایند تغییر فشار و حجم گاز به سرعت صورت پذیرفته و دمای گاز به همان نسبت تغییر میکند(دمای متغیر گاز)
فرایند انقباض و انبساط در یک آکومولاتور پیستونی هیدرولیک تابع قوانین تغییرات پلی تروپیک در حالت گاز هستند. برای گازهای ایده ال فرمول زیر در مورد رابطه فشار و حجم گاز صادق است:
دراین فرمول عامل زمان با نماد n (توان پلی تروپیک) مشخص میشود. برای گاز نیتروژن در یک فرایند ایزوترمال n=1 و برای فرایند آدیاباتیک n=1.4 در نظر گرفته میشود.
حجم روغن ورودی و خروجی آکومولاتور پیستونی هیدرولیک براساس اینکه فرایند انقباض و انبساط گاز بصورت ایزوترمال یا آدیاباتیک اتفاق بیفتد متفاوت است. در فرایند ایزوترمال، حجم روغن قابل ذخیره و تحویل آکومولاتور نسبت به فرایند آدیاباتیک بیشتر است. این امر ناشی از فشردگی و انبساط بیشتر حجم گاز در فرایند ایزوترمال است.
با کمک فرمولهای زیر میتوان حجم روغن قابل ذخیره در آکومولاتور(∆V) را محاسبه کرد:
t0 = دمای گاز در فشار شارژ اولیه | V0 = حجم گاز در فشار شارژ اولیه | P0 = فشار اولیه شارژ گاز |
t1 = دمای گاز در حداقل فشار کاری | V1 = حجم گاز در حداقل فشار کاری | P1 = حداقل فشار کاری |
t2 = دمای گاز در حداکثر فشار کاری | V2 = حجم گاز در حداکثر فشار کاری | P2 = حداکثر فشار کاری |
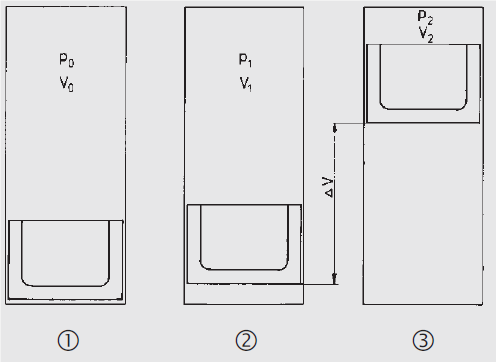


فرایند پلی تروپیک | ![]() |
فرایند ایزوترمال(n=1) | ![]() |
فرایند آدیاباتیک(n=1.4) | ![]() |
NSK-350
حداکثر فشار : 350 بار
حداکثر حجم روغن : 100 لیتر
نوع سیل های هیدرولیک باید براساس شرایط کاری سیستم شامل: سرعت، بسامد کاری، نوع سیال و دما انتخاب شوند.
* برای اطلاعات بیشتر به بخش سیل های هیدرولیک مراجعه کنید یا با واحد فنی شرکت تماس حاصل نمائید.
دانلود کاتالوگ محصول
1- مشخصات اصلی :
- - ظرفیت حجمی متنوع تا حداکثر گنجایش ذخیره روغن 100 لیتر
- - صرفه جویی در مصرف توان سیستم هیدرولیک
- - کمترین میزان اشغال فضا نسبت به حجم ذخیره روغن
- - امکان مانیتور کردن موقعیت حرکت پیستون
- - طول عمر بالا ، نگهداری و تعمیر آسان
- - حداکثر سرعت حرکت پیستون تا 5 متر بر ثانیه
- - قابلیت کارکرد در دماهای بالای روغن (تا 180 درجه سلسیوس)
2- خصوصیات عملکردی :
مدل کد | NSK-350 | |||||||||
حداکثر حجم ذخیره روغن (لیتر بر دقیقه) | 100 | 50 | 20 | 10 | 7.5 | 5 | 2 | 1 | 0.5 | 0.2 |
فشار کاری(بار) | 10÷350 | |||||||||
نوع سیال | روغن های پایه معدنی (برای سایر روغن ها نظیر واتر گلیکول یا فسفات استر با واحد فنی شرکت تماس بگیرید) | |||||||||
ویسکوزیته روغن | ISO VG 15÷100 | |||||||||
سطح تمیزی روغن | ISO 19/16 | |||||||||
محدوده دمای روغن | -20˚C +80˚C | |||||||||
محدوده دمای محیط | -20˚C +70˚C |
3- نحوه کدگذاری :
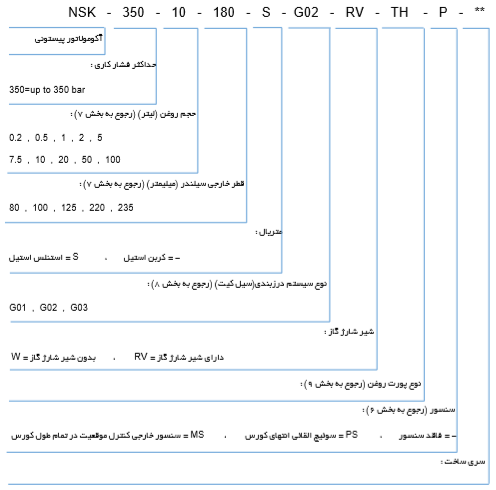
4- موقعیت نصب:
آکومولاتورهای پیستونی هیدرولیک در هر موقعیتی از نصب کار میکنند. اما ترجیح آنست که بصورت عمودی قرار گیرند بطوریکه محفظه گاز بالا قرار گیرد. به این ترتیب از رسوب کردن آلودگی موجود در روغن هیدرولیک بر روی سیل ها جلوگیری میشود. آکومولاتورهای دارای سنسور الکتریکی موقعیت سنج بهترست بصورت عمودی نصب گردند.
5- شارژ گاز:
نیتروژن با خلوص %99.99 با سطح تمیزی > 3 میکرون استفاده شود. هرگز از اکسیژن استفاده نکنید(خطر انفجار!)
6- امکان مانیتورینگ موقعیت پیستون:
PS = سوئیچ القائی الکتریکی: عموما این نوع سنسور برای مشخص کردن زمانیکه آکومولاتور پیستونی در حداکثر شارژ روغن قرار دارد بکار میرود. همچنین با تنظیم این سنسور میتوان مشخص کرد که سایر شیرالات و ادوات کنترلی هیدرولیک در چه کورسی از حرکت پیستون(بعبارتی در چه میزان از شارژ روغن) آکومولاتور در کنترل مدار هیدرولیک اثر بگذارند. هرچند که موقعیت نصب آکومولاتور پیستونی بر عملکرد سنسور اثرگذار نیست، اما ترجیح آنست که با توجه به وجود اصطکاک و احتمال فرسودگی و استهلاک گاید مربوط به شافت سنسور، آکومولاتور پیستونی دارای سنسور القائی در حالت عمودی نصب شود. (حداکثر سرعت حرکت پیستون 0.5 متر بر ثانیه)
MS = سنسور خارجی کنترل موقعیت پیستون: این سنسور این امکان را میدهد که موقعیت پیستون در تمام طول کورس حرکت آن قابل پایش باشد. بصورت استاندارد سنسور موقعیت سنج در سمت محفظه روغن و در مرکز درپوش نصب میشود و پورت اتصال هیدرولیک بصورت خارج از مرکز بر روی درپوش تعبیه میگردد. البته در موارد خاص و در صورت لزوم امکان نصب سنسور بر روی درپوش سمت گاز وجود دارد. آکومولاتور پیستونی هیدرولیک دارای سنسور موقعیت سنج را میتوان در هر حالتی نصب کرد(عمودی/افقی) فقط باید توجه کرد که فضای کافی برای حرکت شافت سنسور به سمت خارج(به اندازه طول کورس پیستون) وجود داشته باشد. جهت دستیابی به دقت بالا در سنجش موقعیت، بهترست حداکثر سرعت حرکت پیستون بیشتر از 0.5 متر بر ثانیه نباشد.
7- ابعاد کلی و نصب :
وزن (کیلو) | B | A | حداکثر فشار کاری (بار) | حجم اسمی (لیتر) | مدل کد | ![]() |
7 | 80 | 218 | 350 | 0.2 | ![]() |
|
9 | 80 | 325 | 350 | 0.5 | ||
12 | 100 | 350 | 350 | 1 | ||
18 | 100 | 550 | 350 | 2 | ||
40 | 125 | 850 | 350 | 5 | ||
50 | 125 | 1170 | 350 | 7.5 | ||
105 | 220 | 655 | 350 | 10 | ||
130 | 220 | 1050 | 350 | 20 | ||
250 | 220 | 2225 | 350 | 50 | ||
380 | 235 | 3490 | 350 | 100 |
8- نوع سیل(درزبند) هیدرولیک :
کد سیل کیت | جنس آببندها | محدوده دمای کاری(براساس نوع روغن) ˚C | حداکثر سرعت حرکت m/s |
G01 | PU , PTFE , NBR | HL, HLP(-30 +100) , HFC(-20 +60) | 0.5 |
G02 | PTFE , NBR | HL, HLP(-30 +100) , HFC(-20 +60) | 1 |
G03 | PTFE , FKM | HFDR(-30 +150) | 5 |
G04 | PTFE , NBR | HL, HLP(-30 +105) , HFC (-20 +60) | 5 |
9- پورت(دهانه) روغن :
- مدل رزوه ای
- مدل فلانجی
L | K | J | H | G | F | E | D | C | B | A | Type |
G3 | G2,1/2 | G2 | G1,1/2 | G1,1/4 | G1 | G3/4 | G1/2 | G3/8 | G1/4 | G1/8 | A |
M60x2 | M48x2 | M42x2 | M33x2 | M27x2 | M22x1.5 | M18x1.5 | M16x1.5 | M14x1.5 | M12x1.5 | M10x1 | B |
K | J | H | G | F | E | D | C | B | A | Type |
DN200 | DN150 | DN125 | DN100 | DN80 | DN65 | DN50 | DN40 | DN25 | DN15 | A |
آکومولاتور پیستونی هیدرولیک
سیالات تقریبا غیر قابل فشرده سازی هستند و نمیتوانند انرژی را بصورت فشار ذخیره کنند. به همین دلیل در آکومولاتورهای هیدرونیوماتیک از قابلیت فشرده سازی یک گاز(مانند نیتروژن) برای ذخیره کردن سیال(روغن هیدرولیک) استفاده میشود. آکومولاتورهای پیستونی بر مبنای همین قاعده ساخته میشوند. یک آکومولاتور پیستونی عبارتست از یک محفظه روغن و یک محفظه گاز به همراه یک پیستون که بعنوان یک واسطه درزبندی شده میان دو محفظه عمل میکند. بخش حاوی گاز با نیتروژن شارژ اولیه میشود. بخش حاوی روغن به مدار هیدرولیک متصل میگردد بطوریکه با افزایش فشار در سیستم، روغن وارد آکومولاتور شده و گاز را فشرده میکند. هنگام کاهش فشار در سیستم، گاز فشرده شده منبسط شده و روغن ذخیره شده وارد مدار هیدرولیک میگردد.
مزایای کاربرد آکومولاتور پیستونی هیدرولیک:
|
نمونه پروژه های انجام شده
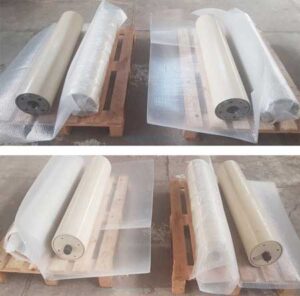

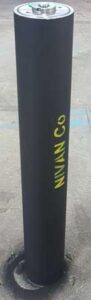
NCC
مطابق با ISO 6022
حداکثر فشار کاری : 320 بار
* نکاتی در رابطه با جدول ابعادی شماره 5
بطور استاندارد برای تمام انواع نصب، پورت روغن در موقعیت شماره 1 و کوشنینگ قابل تنظیم در موقعیت شماره 3 قرار میگیرند.
نوع سیل های هیدرولیک باید براساس شرایط کاری سیستم شامل: سرعت، بسامد کاری، نوع سیال و دما انتخاب شوند.
انواع سیل ها برای شرایط خاص کاری از جمله دمای بسیار بالا، سرعت حرکت زیاد، فرکانس حرکتی بالا یا کاربردهای سنگین قابل ارائه هستند. تمام درزبندها، استاتیک یا دینامیک، بصورت دوره ای باید تعویض شوند. بعنوان یک قاعده کلی، مناسبترین دمای روغن در سیستم های هیدرولیک حدود 40 درجه سانتیگراد است.
* برای اطلاعات بیشتر به بخش سیل های هیدرولیک مراجعه کنید یا با واحد فنی شرکت تماس حاصل نمائید.
دانلود کاتالوگ محصول
1- مشخصات کلی :
- - سیلندرهای هیدرولیک سری NCC از نوع دوطرفه و مخصوص استفاده در کاربردهای صنعتی هستند. طراحی مخصوص آنها تضمین کننده عملکرد مناسب و طول عمر بالای آنهاست.
- - قطر پیستون از 50 تا 320 میلی متر
- - حداکثر کورس حرکتی 5000 میلی متر
- - 4 روش نصب استاندارد
- - 4 نوع سیستم درزبندی (سیل کیت) هیدرولیک
- - امکان نصب کوشنینگ(ترمز هیدرولیکی) ثابت یا قابل تنظیم
- - امکان نصب سنسور موقعیت سنج(پوزیشن ترنسدوسر) داخلی و سوئیچ حدی(پراکسیمیتی سنسور)
2- خصوصیات عملکردی :
حداکثر فشار کاری | 320 bar |
حداقل فشار کاری | 10 bar |
نوع سیال | روغن های پایه معدنی (برای سایر روغن ها نظیر واتر گلیکول یا فسفات استر با واحد فنی شرکت تماس بگیرید) |
ویسکوزیته روغن | ISO VG 15÷100 |
سطح تمیزی روغن | ISO 19/16 |
محدوده دمای روغن | -20˚C +80˚C |
محدوده دمای محیط | -20˚C +80˚C |
موقعیت نصب | بدون محدودیت |
حداکثر سرعت پیستون | 5 m/s |
3- نحوه کدگذاری :
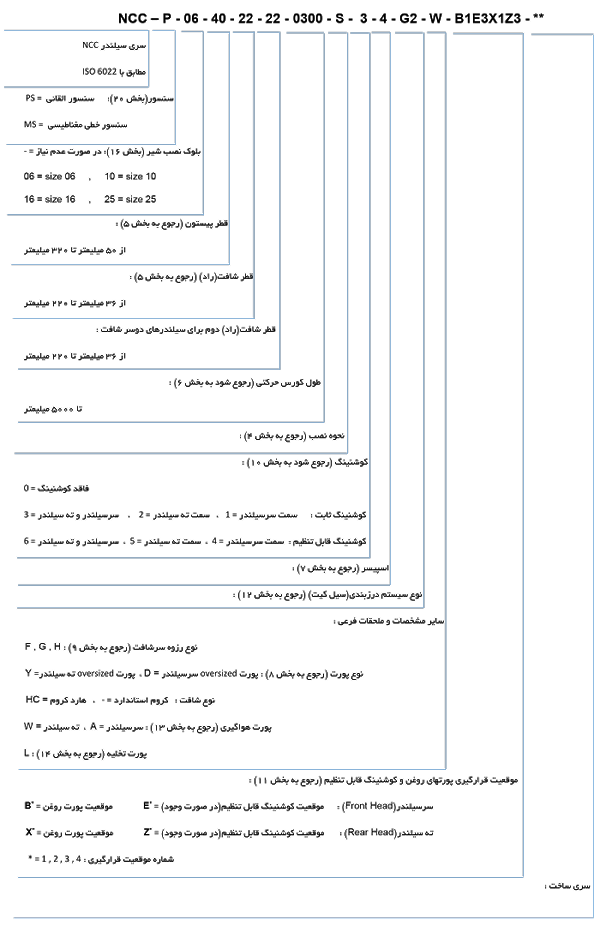
4- نحوه نصب :
X = basic mounting | |
![]() |
![]() |
A (ISO MF3) = front round flange mounting | |
![]() |
![]() |
B (ISO MF4) = rear round flange mounting | |
![]() |
![]() |
L (ISO MT4) = intermediate trunnion mounting | |
![]() |
![]() |
S (ISO MP5) = fixed eye with spherical bearing mounting | |
![]() |
![]() |
5- ابعاد نصب :
قطر پیستون | 50 | 63 | 80 | 100 | 125 | 140 | 160 | 180 | 200 | 250 | 320 | |
شافت | 36 | 45 | 56 | 70 | 90 | 90 | 110 | 110 | 140 | 180 | 220 | |
a.B | 32.5°.25° | 32°.26° | 35°.20° | 35°.20° | 35°.20° | 27.5°.17.5 | 25°.20° | 25°.20° | 25°.20° | 27°.18° | 25°.20° | |
AA | 90 | 105 | 128 | 152 | 188 | 215 | 241 | 275 | 295 | 365 | 458 | |
B/BA f8/h8 | 63 | 75 | 90 | 110 | 132 | 145 | 160 | 185 | 200 | 250 | 320 | |
BG min | 20 | 23 | 23 | 30 | 33 | 33 | 43 | 40 | 40 | 58 | 70 | |
CX H7 | 32 | 40 | 50 | 63 | 80 | 90 | 100 | 110 | 125 | 160 | 200 | |
D | 29 | 36 | 36 | 42 | 42 | 52 | 52 | 52 | 52 | 58 | 58 | |
D1 | 36 | 42 | 42 | 52 | 52 | 58 | 58 | 58 | 58 | 69 | 69 | |
E max | 108 | 124 | 148 | 175 | 214 | 255 | 270 | 315 | 330 | 412 | 510 | |
EE (1) 6g | G 1/2 | G 3/4 | G 3/4 | G 1 | G 1 | G 1 1/4 | G 1 1/4 | G 1 1/4 | G 1 1/4 | G 1 1/2 | G 1 1/2 | |
EE1 (1) 6g | G 3/4 | G 1 | G 1 | G 1 1/4 | G 1 1/4 | G 1 1/2 | G 1 1/2 | G 1 1/2 | G 1 1/2 | G 2 | G 2 | |
EP | 27 | 35 | 40 | 52 | 66 | 65 | 84 | 88 | 102 | 130 | 162 | |
EX h12 | 32 | 40 | 50 | 63 | 80 | 90 | 100 | 110 | 125 | 160 | 200 | |
FB H13 | 13.5 | 13.5 | 17.5 | 22 | 22 | 26 | 26 | 33 | 33 | 39 | 45 | |
FC js13 | 132 | 150 | 180 | 212 | 250 | 300 | 315 | 365 | 385 | 475 | 600 | |
LT min | 40 | 50 | 63 | 71 | 90 | 113 | 112 | 135 | 160 | 200 | 250 | |
MS max | 40 | 50 | 63 | 71 | 90 | 113 | 112 | 118 | 160 | 200 | 250 | |
MT | 30 | 50 | 85 | 152 | 255 | 255 | 304 | 370 | 490 | 950 | 1750 | |
NF js13 | 25 | 28 | 32 | 36 | 40 | 40 | 45 | 50 | 56 | 63 | 80 | |
PJ | 120 | 133 | 155 | 171 | 205 | 208 | 235 | 250 | 278 | 325 | 350 | |
RT | n°8 holes M8 | n°8 holes M10 | n°8 holes M12 | n°8 holes M14 | n°8 holes M16 | n°8 holes M16 | n°8 holes M18 | n°8 holes M20 | n°8 holes M22 | n°8 holes M27 | n°8 holes M33 | |
TD f8 | 32 | 40 | 50 | 63 | 80 | 90 | 100 | 110 | 125 | 160 | 200 | |
TL js13 | 25 | 32 | 40 | 50 | 63 | 70 | 80 | 90 | 100 | 125 | 160 | |
TM h12 | 112 | 125 | 150 | 180 | 224 | 265 | 280 | 320 | 335 | 425 | 680 | |
UC max | 160 | 180 | 215 | 260 | 300 | 340 | 370 | 425 | 455 | 545 | 850 | |
UM | 162 | 189 | 230 | 280 | 350 | 405 | 440 | 500 | 535 | 675 | 850 | |
UV max | 108 | 124 | 150 | 180 | 219 | 260 | 280 | 315 | 333 | 412 | 510 | |
VD | 4 | 4 | 4 | 5 | 5 | 5 | 5 | 5 | 5 | 8 | 8 | |
VE max | 29 | 32 | 36 | 41 | 45 | 45 | 50 | 55 | 61 | 71 | 88 | |
WC | 22 | 25 | 28 | 32 | 36 | 36 | 40 | 45 | 45 | 50 | 56 | |
WF | 47 | 53 | 60 | 68 | 76 | 76 | 85 | 95 | 101 | 113 | 136 | |
XO | 305 | 348 | 395 | 442 | 520 | 580 | 617 | 690 | 756 | 903 | 1080 | |
XV | Min stroke style l | 175 | 185 | 150 | 160 | 245 | 250 | 260 | 350 | 390 | 460 | 560 |
min | 260 | 285 | 290 | 320 | 410 | 440 | 465 | 540 | 590 | 690 | 820 | |
max | 85+ stroke | 100+ stroke | 140+ stroke | 160+ stroke | 165+ stroke | 190+ stroke | 205+ stroke | 190+ stroke | 200+ stroke | 230+ stroke | 260+ Stroke | |
Y ±2 | 98 | 112 | 120 | 134 | 153 | 181 | 185 | 205 | 220 | 260 | 310 | |
ZB max | 244 | 274 | 305 | 340 | 396 | 430 | 467 | 505 | 550 | 652 | 764 | |
ZP | 265 | 298 | 332 | 371 | 430 | 465 | 505 | 550 | 596 | 703 | 830 |
- 1) پورتهای روغن بصورت رزوه ای مطابق با استاندارد GAS با اندازه نشیمنگاه D (counterbore) براساس استاندارد ISO 1179-1 بر روی سیلندر تعبیه میگردند. در صورتیکه پورتهای بزرگتر از استاندارد(oversized ports) مدنظر باشند ، ابعاد D و EE به ترتیب با ابعاد D1 و EE1 جایگزین میشوند.
- 2) مقدار E نشاندهنده قطر سرسیلندر و ته سیلندر برای تمام انواع روشهای نصب سیلندر هستند، مگراینکه در بخش 2 مقدار متفاوتی برای آن ذکر شده باشد.
- 3) مقدار MT نمایانگر گشتاور سفت کردن پیچ هاست. پیچ ها دارای حداقل گرید 10.9 براساس ISO 898/2 هستند.
- 4) برای نوع نصب L (ترونیون) طول کورس حرکتی باید دستکم چند میلی متر بیشتر از حداقل مقدار XV ذکر شده باشد. همچنین طول XV باید عددی میان XVmin و XVmax باشد و هنگام سفارش گذاری بطور جداگانه مقدار آن به میلی متر ذکر شود.
- 5) تلرانس ابعادی مطابق جدول ذیل است:
ابعاد نصب ZP , XO , PJ WF , WC , XV کورس حرکت < 1250 ±1.5 ±2 1250< کورس حرکت < 3150 ±3 ±4 3150< کورس حرکت ±5 ±8
6- کورس حرکت :
باید طول کورس حرکتی سیلندر بگونه ای تعیین شود که اندکی از کورس واقعی مورد نیاز آن بیشتر باشد. بدین ترتیب از برخورد پیستون به سرسیلندر و ته سیلندر در انتهای کورس رفت و برگشت جلوگیری میشود.
حداقل طول کورس (میلیمتر)
حداکثر طول کورس حرکتی سیلندر : 5000 میلی متر
تلرانس کورس حرکتی : 0 +2 mmبرای طول کورس تا 1250 میلی متر
0 +5 mm برای طول کورس از 1250 تا 3150 میلی متر
0 +8 mmبرای طول کورس بیشتر از 3150 میلی متر
320 | 250 | 200 | 180 | 160 | 140 | 125 | 100 | 80 | 63 | 50 | Bore |
120 | 80 | 70 | 70 | 50 | 50 | 50 | 25 | 20 | 70 | 70 | Minimum Stroke |
7- اسپیسر :
برای سیلندرهای هیدرولیک با طول کورس بیشتر از 1000 میلی متر -که بصورت فشاری کار می کنند- اسپیسرهایی در کنار پیستون قرار میگیرند. افزودن اسپیسر، طول کلی سیلندر را افزایش میدهد. به همین خاطر مطابق جدول ذیل، مقدار طول اسپیسر باید به ابعادی از سیلندر که وابسته به طول کورس هستند افزوده شود. برای سیلندرهایی که بصورت کششی کار میکنند میتوان اسپیسر را حذف نمود.
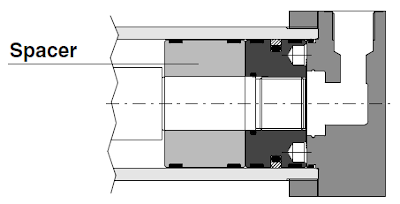
2501 ÷ 5000 | 2001 ÷ 2500 | 1501 ÷ 2000 | 1001 ÷ 1500 | طول کورس (میلی متر) |
8 | 6 | 4 | 2 | کد اسپیسر |
200 | 150 | 100 | 50 | طول (میلی متر) |
8- پورت(دهانه) روغن از نوع فلانج SAE 6000 – مطابق ISO 6162-2
پورت روغن بصورت فلانج، سبب تسهیل اتصال سیلندر به لوله کشی سیستم میشود. حداکثر فشار کاری آن 320 بار است.
* برای نوع نصب B(ISO MF4) امکان نصب فلانجی وجود ندارد.
** با ISO 6162-2 مطابقت ندارد.
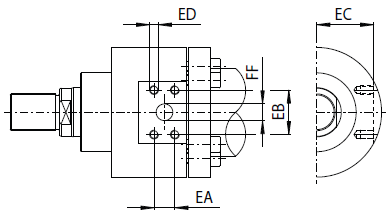
Bore | DN | EC | EA ±0.25 | EB ±0.25 | ED 6g | FF 0/-1.5 |
50* | 13 | 46 | 18.2 | 40.5 | M8x1.25 | 13 |
63* | 19 | 51 | 23.8 | 50.8 | M10x1.5 | 19 |
80 | 65 | |||||
100 | 25 | 77 | 27.8 | 57.2 | M12x1.75 | 25 |
125 | 99 | |||||
140 | 32 | 118 | 31.6 | 66.6 | M14x2** | 32 |
160 | 126 | |||||
180 | 150 | |||||
200 | 158 | |||||
250 | 38 | 195 | 36.7 | 79.3 | M16x2 | 38 |
320 | 51 | 245 | 44.5 | 96.8 | M20x2.5 | 51 |
9- ابعاد رزوه و سرشفت :
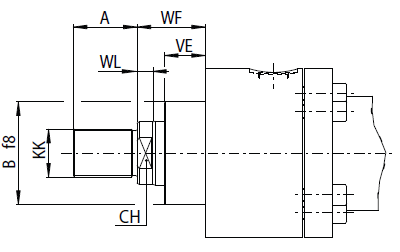
Bore | 50 | 63 | 80 | 100 | 125 | 140 | 160 | 180 | 200 | 250 | 320 |
Rod | 36 | 45 | 56 | 70 | 90 | 90 | 110 | 110 | 140 | 180 | 220 |
A max | 36 | 45 | 56 | 63 | 85 | 90 | 95 | 105 | 112 | 125 | 160 |
CH | 30 | 39 | 48 | 62 | 80 | 75 | 100 | 100 | 128 | 15 | 20 |
KK 6g | M27x2 | M33x2 | M42x2 | M48x2 | M64x3 | M27x3 | M80x3 | M90x3 | M100x3 | M125x4 | M160x4 |
WL min | 8 | 10 | 10 | 10 | 15 | 15 | 15 | 15 | 15 | - | - |
10- کوشنینگ (ترمز هیدرولیکی) :
استفاده از کوشنینگ برای کاربردهای ذیل توصیه میشود:
- • زمانیکه سرعت طی کورس حرکتی، بیشتر از 0.05 m/s باشد.
- • هنگامیکه ضروری است سر و صدا و شوک های مکانیکی کاهش یابد.
- • کاربردهایی که سیلندر بصورت عمودی عمل کرده و بار خارجی زیادی بر روی آن قرار دارد.
![]() |
![]() |
![]() |
||
![]() |
320 | 250 | 200 | 180 | 160 | 140 | 125 | 100 | 80 | 63 | 50 | قطر پیستون | |
180 | 180 | 140 | 110 | 110 | 90 | 90 | 70 | 56 | 45 | 36 | قطر شافت | |
80 | 80 | 64 | 64 | 64 | 60 | 60 | 50 | 45 | 40 | 29 | Lf جلو | طول کوشنینگ (میلیمتر) |
64 | 64 | 64 | 64 | 64 | 60 | 60 | 50 | 45 | 38 | 35 | Lf عقب |
11- موقعیت قرارگیری پورتهای روغن و کوشنینگ قابل تنظیم :
سرسیلندر(Front Head) : | :موقعیت کوشنینگ قابل تنظیم = E3 | موقعیت پورت روغن = B1 |
ته سیلندر(Rear Head) : | موقعیت کوشنینگ قابل تنظیم = Z3 | موقعیت پورت روغن = X1 |
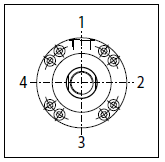
12- نوع سیل(درزبند) هیدرولیک :
حداکثر سرعت حرکت m/s | محدوده دمای کاری(براساس نوع روغن) ˚C | جنس آببندها | کد سیل کیت |
0.5 | HL, HLP(-30 +100) , HFC(-20 +60) | PU , TPE , NBR , POM | G0 |
0.5 | HL, HLP(-30 +100) , HFC(-20 +60) | PU , PTFE , NBR | G1 |
5 | HL, HLP(-30 +100) , HFC(-20 +60) | PTFE , NBR | G2 |
5 | HFDR(-30 +150) | PTFE , FKM | G3 |
0.5 | HL, HLP(-30 +105) , HFC (-20 +60) | PU/NBR , POM , NBR | G4 |
13- پورت (شیر) هواگیری :
پورت هواگیری سرسیلندر = A پورت هواگیری ته سیلندر = W
برای جلوگیری از ایجاد سر و صدا، لرزش و حرکت غیرعادی سیلندر، باید هوا از سیستم هیدرولیک خارج شود. برای تحقق این امر، راحتترین و ایمن ترین روش، استفاده از شیرهای مخصوص هواگیری است. بطور استاندارد برای تمام انواع نصب سیلندر، پورت هواگیری در موقعیت 3 قرار میگیرد.
NCN
مطابق با ISO 6020-1
حداکثر فشار کاری : 250 بار
* نکاتی در رابطه با جدول ابعادی شماره 6
بطور استاندارد برای تمام انواع نصب سیلندر بغیر از نوع نصب E، پورت روغن در وجه شماره 1 و کوشنینگ قابل تنظیم در وجه شماره 3 قرار میگیرند. برای نوع نصب E در صورتیکه کوشنینگ قابل تنظیم درنظر گرفته شده باشد، در وجه شماره 2 قرار میگیرد(موقعیت های Z* و E*).
دانلود کاتالوگ محصول
1- مشخصات کلی :
- - سیلندرهای هیدرولیک سری NCN از نوع دوطرفه و مخصوص استفاده در کاربردهای صنعتی هستند. طراحی مخصوص آنها تضمین کننده عملکرد مناسب و طول عمر بالای آنهاست.
- - قطر پیستون از 40 تا 200 میلی متر
- - امکان انتخاب از میان دو سایز شافت برای هر قطر پیستون
- - حداکثر کورس حرکتی 5000 میلی متر
- - 8 روش نصب استاندارد
- - 4 نوع سیستم درزبندی هیدرولیک(سیل کیت)
- - امکان نصب کوشنینگ(ترمز هیدرولیکی) ثابت یا قابل تنظیم
- - امکان نصب سنسور موقعیت سنج(پوزیشن ترنسدوسر) داخلی و سوئیچ حدی(پراکسیمیتی سنسور)
2- خصوصیات عملکردی :
حداکثر فشار کاری | 250 bar |
حداقل فشار کاری | 10 bar |
نوع سیال | روغن های پایه معدنی (برای سایر روغن ها نظیر واتر گلیکول یا فسفات استر با واحد فنی شرکت تماس بگیرید) |
ویسکوزیته روغن | ISO VG 15÷100 |
سطح تمیزی روغن | ISO 19/16 |
محدوده دمای روغن | -20˚C +80˚C |
محدوده دمای محیط | -20˚C +80˚C |
موقعیت نصب | بدون محدودیت |
پوشش | رنگ روغنی RAL |
حداکثر سرعت پیستون | 5 m/s |
3- نحوه کدینگ :
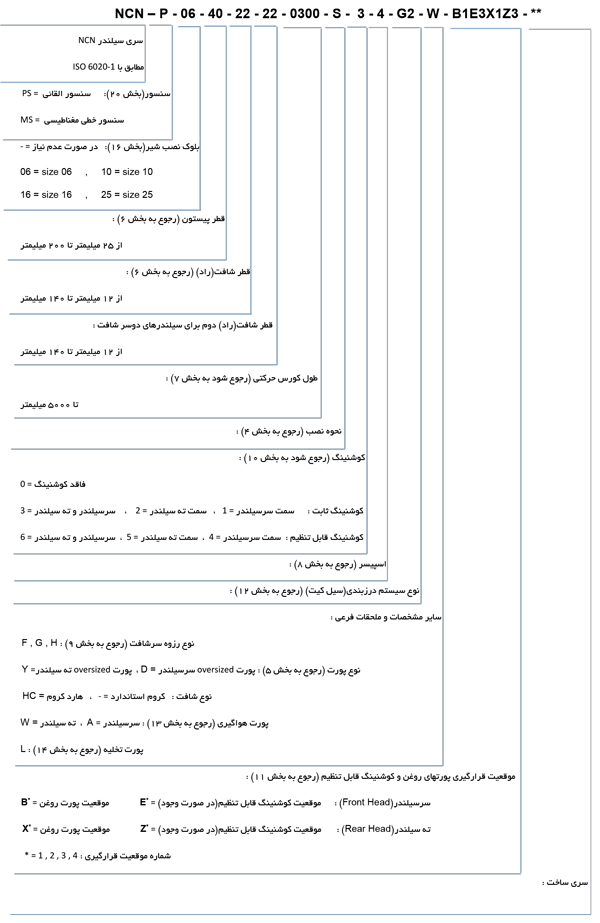
4- نحوه نصب :
X = basic mounting | |
![]() |
![]() |
A (ISO MF3) = front round flange mounting | |
![]() |
![]() |
B (ISO MF4) = rear round flange mounting | |
![]() |
![]() |
N (ISO MF1) = front square flange mounting (not for bores 160-200) | |
![]() |
![]() |
P (ISO MF2) = rear square flange mounting (not for bores 160-200) | |
![]() |
![]() |
L (ISO MT4) = intermediate trunnion mounting | |
![]() |
![]() |
E (ISO MS2) = side feet mounting | |
![]() |
![]() |
S (ISO MP5) = fixed eye with spherical bearing mounting | |
![]() |
![]() |
D (ISO MP3) = fixed eye mounting | |
![]() |
![]() |
5- پورت(دهانه) روغن از نوع فلانج SAE 3000 – مطابق ISO 6162-1

FF -1.5 / 0 | ED 6g | EB ±0.25 | EA ±0.25 | EC | DN | قطر پیستون |
13 | M8x1.25 | 38.1 | 17.5 | 50 | 13 | 63 |
58 | 80 | |||||
19 | M10x1.5 | 47.6 | 22.3 | 71 | 19 | 100 |
89 | 125 | |||||
25 | M10x1.5 | 52.4 | 26.2 | 113 | 25 | 160 |
137 | 200 |
- • ابعاد به میلی متر هستند.
- • برای قطر پیستون 40 و 50 میلی متر امکان تعبیه پورت فلانجی SAE 3000 وجود ندارد.
6- ابعاد نصب :
قطر پیستون | 40 | 50 | 63 | 80 | 100 | 125 | 160 | 200 | ||
شافت | standard | 22 | 28 | 36 | 45 | 56 | 70 | 90 | 110 | |
Differential | 28 | 36 | 45 | 56 | 70 | 90 | 110 | 140 | ||
B/BA f8/H8 | 50 | 60 | 70 | 85 | 106 | 132 | 160 | 200 | ||
CD/CX H9/H7 | 20 | 25 | 32 | 40 | 50 | 63 | 80 | 100 | ||
D (1) min | 29 | 29 | 36 | 36 | 42 | 42 | 52 | 52 | ||
D1 (1) min | 36 | 36 | 42 | 42 | 52 | 52 | 58 | 58 | ||
E (2)max | 78 | 95 | 116 | 130 | 158 | 192 | 238 | 285 | ||
EE (1) | G 1/2 | G 1/2 | G 3/4 | G 3/4 | G 1 | G 1 | G 1 1/4 | G 1 1/4 | ||
EE1 (1) | G 3/4 | G 3/4 | G 1 | G 1 | G 1 1/4 | G 1 1/4 | G 1 1/2 | G 1 1/2 | ||
EH max | 82 | 100 | 120 | 135 | 161 | 196 | 238 | 288 | ||
EP | 18 | 22 | 27 | 35 | 40 | 52 | 66 | 84 | ||
EX h12 | 20 | 25 | 32 | 40 | 50 | 63 | 80 | 100 | ||
F max | 80 | 100 | 120 | 135 | 160 | 195 | NA | NA | ||
FB H13 | 9 | 11 | 13.5 | 17.5 | 22 | 22 | 22 | 26 | ||
FC js13 | 106 | 126 | 145 | 165 | 200 | 235 | 280 | 340 | ||
LH h10 | 43 | 52 | 62 | 70 | 82 | 100 | 119 | 145 | ||
LT min | 25 | 32 | 40 | 50 | 63 | 71 | 90 | 112 | ||
MS max | 25 | 32 | 40 | 50 | 63 | 71 | 90 | 112 | ||
MT Nm(3) | 40 | 78 | 137 | 78 | 137 | 226 | 471 | 471 | ||
NF js13 | 16 | 20 | 25 | 32 | 32 | 32 | 36 | 40 | ||
PJ (5) | 97 | 111 | 117 | 134 | 162 | 174 | 191 | 224 | ||
R js13 | 40.6 | 48.2 | 55.5 | 63.1 | 76.5 | 90.2 | NA | NA | ||
S js13 | 25 | 32 | 32 | 40 | 50 | 56 | 60 | 72 | ||
SB H13 | 11 | 14 | 18 | 22 | 26 | 33 | 33 | 39 | ||
SS (5) | 183 | 199 | 211 | 236 | 293 | 321 | 364 | 447 | ||
TD f8 | 20 | 25 | 32 | 40 | 50 | 63 | 80 | 100 | ||
TE js13 | 78 | 95 | 116 | 130 | 158 | 192 | 238 | 285 | ||
TF js13 | 98 | 116.4 | 134 | 152.5 | 184.8 | 217.1 | NA | NA | ||
TL js13 | 16 | 20 | 25 | 32 | 40 | 50 | 63 | 80 | ||
TM h12 | 90 | 105 | 120 | 135 | 160 | 195 | 240 | 295 | ||
TS js13 | 100 | 120 | 150 | 170 | 205 | 245 | 295 | 350 | ||
UC max | 125 | 148 | 170 | 195 | 238 | 272 | 316 | 385 | ||
UF max | 115 | 140 | 160 | 185 | 225 | 255 | NA | NA | ||
UM | 122 | 145 | 170 | 199 | 240 | 295 | 366 | 455 | ||
US max | 120 | 145 | 180 | 210 | 250 | 300 | 350 | 415 | ||
UV | 90 | 108 | 124 | 150 | 180 | 219 | 280 | 333 | ||
VD | 3 | 4 | 4 | 4 | 5 | 5 | 5 | 5 | ||
WC (5) | 16 | 18 | 20 | 22 | 25 | 28 | 30 | 35 | ||
XO (5) | 231 | 257 | 289 | 332 | 395 | 428 | 505 | 615 | ||
XS (5) | 19.5 | 22 | 29 | 34 | 32 | 32 | 36 | 39 | ||
XV | Minimum stroke | 55 | 55 | 85 | 90 | 110 | 135 | 170 | 190 | |
min | 155 | 160 | 190 | 215 | 255 | 290 | 340 | 420 | ||
max | 100+stroke | 105+stroke | 105+stroke | 125+stroke | 145+stroke | 155+stroke | 170+stroke | 230+stroke |
قطر پیستون | 40 | 50 | 63 | 80 | 100 | 125 | 160 | 200 |
Y (5) | 71 | 72 | 82 | 91 | 108 | 121 | 143 | 190 |
ZD | 215 | 237 | 256 | 290 | 350 | 381 | 430 | 522 |
ZP | 206 | 225 | 249 | 282 | 332 | 357 | 406 | 490 |
ZJ | 190 | 205 | 224 | 250 | 300 | 325 | 370 | 450 |
VE max | 19 | 24 | 29 | 36 | 37 | 37 | 41 | 45 |
WF | 32 | 38 | 45 | 54 | 57 | 60 | 66 | 75 |
ØRod standard | 22 | 28 | 36 | 45 | 56 | 63 | 85 | 95 |
A max | 22 | 28 | 36 | 45 | 56 | 63 | 85 | 95 |
CH | 19 | 22 | 30 | 39 | 48 | 62 | 80 | 100 |
KK 6g | M16x1.5 | M20x1.5 | M27x2 | M33x2 | M42x2 | M48x2 | M64x3 | M80x3 |
ØRod Differents | 28 | 36 | 45 | 56 | 70 | 90 | 110 | 140 |
A max | 28 | 36 | 45 | 56 | 63 | 85 | 95 | 112 |
CH | 22 | 30 | 39 | 48 | 62 | 80 | 100 | 128 |
KK 6g | M20x1.5 | M27x2 | M33x2 | M42x2 | M48x2 | M64x3 | M80x3 | M100x3 |
- 1) پورتهای روغن بصورت رزوه ای مطابق با استاندارد GAS با اندازه نشیمنگاه D (counterbore) براساس استاندارد ISO 1179-1 بر روی سیلندر تعبیه میگردند. در صورتیکه پورتهای بزرگتر از استاندارد(oversized ports) مدنظر باشند ، ابعاد D و EE به ترتیب با ابعاد D1 و EE1 جایگزین میشوند.
- 2) مقدار E نشاندهنده قطر سرسیلندر و ته سیلندر برای تمام انواع روشهای نصب سیلندر هستند، مگراینکه در بخش 2 مقدار متفاوتی برای آن ذکر شده باشد.
- 3) مقدار MT نمایانگر گشتاور سفت کردن پیچ هاست. پیچ ها دارای حداقل گرید 10.9 براساس ISO 898/2 هستند.
- 4) برای نوع نصب L (ترونیون) طول کورس حرکتی باید دستکم چند میلی متر بیشتر از حداقل مقدار XV ذکر شده باشد. همچنین طول XV باید عددی میان XVmin و XVmax باشد و هنگام سفارش گذاری بطور جداگانه مقدار آن به میلی متر ذکر شود.
- 5) تلرانس ابعادی مطابق جدول ذیل است:
ابعاد نصب | ZJ , ZP , XO , SS , PJ | WF , WC , XV , XS , Y |
کورس حرکت < 1250 | ±1.5 | ±2 |
1250< کورس حرکت < 3150 | ±3 | ±4 |
3150< کورس حرکت | ±5 | ±8 |
7- کورس حرکت :
باید طول کورس حرکتی سیلندر بگونه ای تعیین شود که اندکی از کورس واقعی مورد نیاز آن بیشتر باشد. بدین ترتیب از برخورد پیستون به سرسیلندر و ته سیلندر در انتهای کورس رفت و برگشت جلوگیری میشود.
حداکثر طول کورس حرکتی سیلندر : 5000 میلی متر
تلرانس کورس حرکتی : 0 +2 mm برای طول کورس تا 1000 میلی متر
0 +5 mmبرای طول کورس از 1000 تا 3000 میلی متر
0 +8 mmبرای طول کورس بیشتر از 3000 میلی متر
8- اسپیسر :
برای سیلندرهای هیدرولیک با طول کورس بیشتر از 1000 میلی متر -که بصورت فشاری کار می کنند- اسپیسرهایی در کنار پیستون قرار میگیرند. افزودن اسپیسر طول کلی سیلندر را افزایش میدهد. به همین خاطر مطابق جدول ذیل، مقدار طول اسپیسر باید به ابعادی از سیلندر که وابسته به طول کورس هستند افزوده شود.
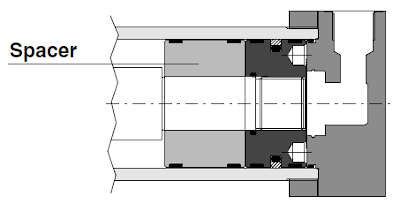
2501 ÷ 5000 | 2001 ÷ 2500 | 1501 ÷ 2000 | 1001 ÷ 1500 | طول کورس (میلی متر) |
8 | 6 | 4 | 2 | کد اسپیسر |
200 | 150 | 100 | 50 | طول (میلی متر) |
9- ابعاد رزوه و سرشفت :
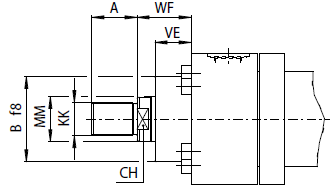
Bore | 40 | 50 | 63 | 80 | 100 | 125 | 160 | 200 |
VE max | 19 | 24 | 29 | 36 | 37 | 37 | 41 | 45 |
WF | 32 | 38 | 45 | 54 | 57 | 60 | 66 | 75 |
ØRod Standard | 22 | 28 | 36 | 45 | 56 | 70 | 90 | 110 |
A max | 22 | 28 | 36 | 45 | 56 | 63 | 85 | 95 |
CH | 19 | 22 | 30 | 39 | 48 | 62 | 80 | 100 |
KK 6g | M16x1.5 | M20x1.5 | M27x2 | M33x2 | M42x2 | M48x2 | M64x3 | M80x3 |
ØRod Differential | 28 | 36 | 45 | 56 | 70 | 90 | 110 | 140 |
A max | 28 | 36 | 45 | 56 | 63 | 85 | 95 | 112 |
CH | 22 | 30 | 39 | 48 | 62 | 80 | 100 | 128 |
KK 6g | M20x1.5 | M27x2 | M33x2 | M42x2 | M48x2 | M64x3 | M80x3 | M100x3 |
10- کوشنینگ (ترمز هیدرولیکی) :
استفاده از کوشنینگ برای کاربردهای ذیل توصیه میشود:
- • زمانیکه سرعت طی کورس حرکتی، بیشتر از 0.05 m/s باشد.
- • هنگامیکه ضروری است سر و صدا و شوک های مکانیکی کاهش یابد.
- • کاربردهایی که سیلندر بصورت عمودی عمل کرده و بار خارجی زیادی بر روی آن قرار دارد.
200 | 160 | 125 | 100 | 80 | 63 | 50 | 40 | قطر پیستون | |||||||||
140 | 110 | 110 | 90 | 90 | 70 | 70 | 56 | 56 | 45 | 45 | 36 | 36 | 28 | 28 | 22 | قطر شافت | |
49 | 34 | 34 | 34 | 27 | 27 | 26 | 26 | 27 | 27 | 29 | 29 | 29 | 29 | 25 | 25 | Lf جلو | طول کوشنینگ (میلیمتر) |
56 | 56 | 41 | 32 | 32 | 32 | 30 | 30 | Lf عقب |
![]() |
![]() |
![]() |

11- موقعیت قرارگیری پورتهای روغن و کوشنینگ قابل تنظیم :
سرسیلندر(Front Head) : | موقعیت کوشنینگ قابل تنظیم = E* | موقعیت پورت روغن = B1 |
ته سیلندر(Rear Head) : | موقعیت کوشنینگ قابل تنظیم = Z* | موقعیت پورت روغن = X1 |
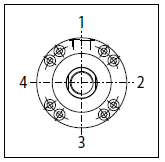
12- نوع سیل(درزبند) هیدرولیک :
<td
کد سیل کیت | جنس آببندها | محدوده دمای کاری(براساس نوع روغن) ˚C | حداکثر سرعت حرکت m/s |
G0 | PU , TPE , NBR , POM | HL, HLP(-30 +100) , HFC(-20 +60) | 0.5 |
G1 | PU , PTFE , NBR | HL, HLP(-30 +100) , HFC(-20 +60) | 0.5 |
G2 | PTFE , NBR | HL, HLP(-30 +100) , HFC(-20 +60) | 5 |
G3 | PTFE , FKM | HFDR(-30 +150) | 5 |
G4 |